Of late, you would have heard of BLDC motors in ceiling fans and other motors that contribute to high-quality energy savings. Yes, BLDC motors can save electricity when compared to induction motors. Let us understand the distinction between these two concepts.
BLDC Motors – Brushless Direct Current Motors
BLDC motors consist of a rotor that includes multiple permanent magnets to generate a DC magnetic field. This magnetic field enters the stator core made up of stacked laminations. While interacting with the current flowing within the windings, it produces a torque interaction between the stator and the rotor, causing the rotor to rotate.
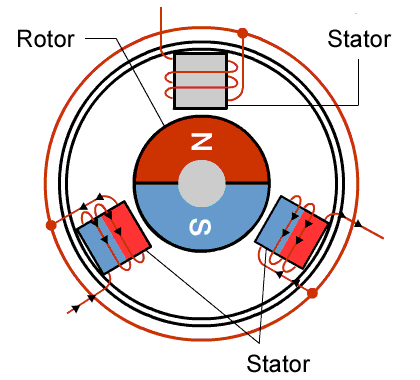
As the rotor rotates, it becomes essential for the magnitude and the polarity of the stator current to vary to ensure that the torque remains constant. Thus, it enhances the efficiency of conversion of mechanical energy to electrical energy.
The device providing the necessary current control is known as an inverter. BLDC motors are useless without this inverter.
Induction Motors – 3-phase AC motors
In a way, the structure of the stators of the BLDC motor and the 3-phase induction motors is the same. Generally, there are three sets of distributed windings inserted within the stator core. The primary difference between the two motors is with the rotor.
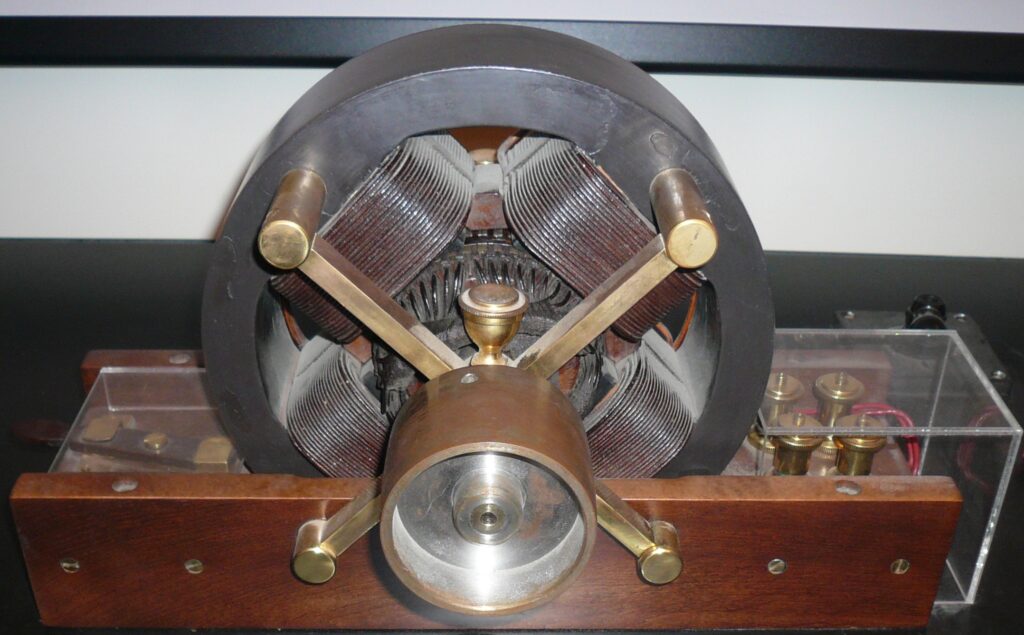
While the BLDC motors have magnets, the inductor rotor does not have any. Instead, it comes as stacked steel laminations with buried peripheral conductors to form a shorted structure. As the current flows through the stator windings, it produces a rotating magnetic field that enters the rotor.
The magnetic field’s frequency as seen by the rotor equals the difference between the rotor’s rotational frequency and the applied electrical frequency. Accordingly, there exists an induced voltage between the shorted structure. It is proportionate to the difference between the electrical and rotor frequency.
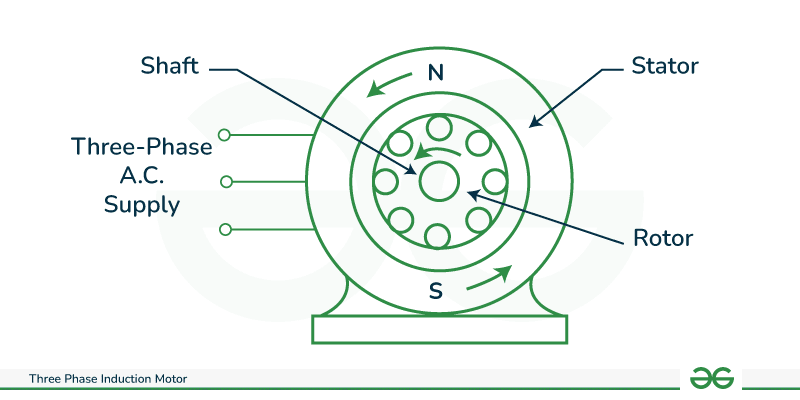
As a response to the induced voltage, currents proportional to the voltage are produced within the rotor conductors. Thus, it accounts for the speed difference. These current flows interact with the original magnetic field to produce force. The desired rotor torque is a component of this force.
BLDC Motors vs Induction Motors
When you connect a 3-phase AC induction motor to a 3-phase power supply, it produces torque. The motor does not require an inverter to start under load. As the induction motor is compatible with conventional utility power, they are popular.
In contrast, the BLDC motors do not have any starting torque when connected to the utility power source. Therefore, it needs an inverter with the phase maintained in step with the rotor’s angular position.
Though induction motors are useful, they have various limitations compared to BLDC motors.
- The 3-phase induction motors cannot operate from DC. Instead, they need an AC supply.
- As the shaft speed is proportional to line frequency, these motors are constant speed machines.
- Compared to DC-type machines, these motors have limited running peak torque capabilities. Further, they have limited torque power when operated from utility power.
- The DC brushless drive generates less heat than the 3-phase SAC induction motors.
It is possible to power an induction machine using an inverter and a battery. Therefore, one can adjust the inverter frequency to vary the motor’s speed. However, the torque performance of such motors is lower than DC machines.
If you add feedback loops to enable the inverter to provide the frequency that the motor desires, these motors can compete with DC and DC brushless motors.
Brushless DC motor | Induction motor |
---|---|
It enables operations at varying speeds with the rated load. The speed characteristics are flat. | The speed characteristics are non-linear, and it enables lower torque at lower speeds. |
It requires a controller to keep the motor running. You can also use the controller for variable speed control. | For fixed speeds, there is no need for a controller. A controller is necessary only if you want variable speed. |
It has permanent magnets on the rotor, so it is possible to achieve a smaller size for given power output. | As both the rotor and stator have windings, the output power is lower than the BLDC motor. |
As the rotor inertia is low, it enables better dynamic characteristics. | The induction motor enables poor dynamic characteristics because of high rotor inertia. |
Thus, you can see that a BLDC motor can produce variable speeds and deliver more power output. It explains why BLDC motors are now in demand in household electrical appliances like washing machines and ceiling fans.